Surgical Stainless Steel Tanks produce almost Zero toxicity, means excellent and safe drinking water, and in 70 years time our grandchildren can use the steel for something else (or en cash it ). Our Multi Layered tank keeps water cool, Zero BP A & S and gives you a toxic free health for generations.
It has inbuilt characteristics of being strong durable and hygiene. These tanks are manufactured through international technology with advance process and quality control with dual protective coating and total wash capability. PNB H2o Plus water tanks gives durable performance while remaining maintenance free in the long run.
Material used for manufacturing the tank is the most preferred raw material used in food and pharmaceutical industries and hence delivers the purest and safest drinking water.
It has inbuilt characteristics of being strong durable and hygiene. These tanks are manufactured through international technology with advance process and quality control with dual protective coating and total wash capability. PNB H2o Plus water tanks gives durable performance while remaining maintenance free in the long run.
Material used for manufacturing the tank is the most preferred raw material used in food and pharmaceutical industries and hence delivers the purest and safest drinking water.

Stainless Steel Tanks
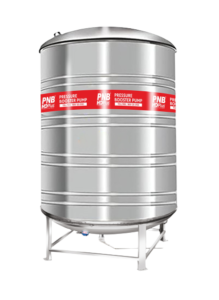







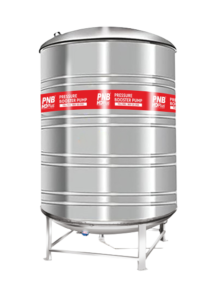

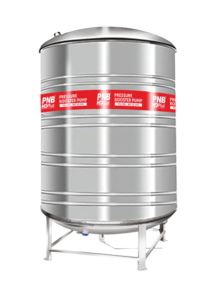



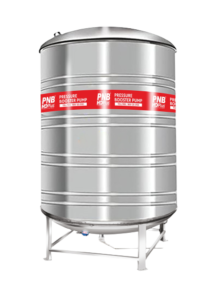

304 - AUSTENITIC STAINLESS STEEL
316L - SURGICAL STAINLESS STEEL
4 Layer Tank
1st layer – 304 / 316L – Surgical Stainless Steel.2nd layer – CCC POWER (Climate Control Coating).
3rd layer – High Density Puff.
4th layer – 304 Austenitic Stainless Steel.
316L - SURGICAL STAINLESS STEEL
316Ti - TITANIUM STAINLESS STEEL
2205 - DUPLEX STAINLESS STEEL
904L - SUPER AUSTENITIC STAINLESS STEEL
5 Layer Tank
1st layer – 316L / 316 Ti/ 2205 Duplex / 904L Stainless Steel.2nd layer – Fire Retardant Thermal Insulation.
3rd layer – GL Panel
4th layer – High Density Pu ff
5th layer – 304 Austenitic Stainless Steel


316L - SURGICAL STAINLESS STEEL
316Ti - TITANIUM STAINLESS STEEL
2205 - DUPLEX STAINLESS STEEL
904L - SUPER AUSTENITIC STAINLESS STEEL
6 Layer Tank
1st layer – 316L / 316Ti / 2205 Duplex / 904L Stainless Steel.2nd layer – Fire Retardant Fire Insulation.
3rd layer – High Density Pu ff.
4th layer – GL Panel.
5th layer – Scrim Wall.
6th layer – 304 Austenitic Stainless Steel.
316L - SURGICAL STAINLESS STEEL
316Ti - TITANIUM STAINLESS STEEL
2205 - DUPLEX STAINLESS STEEL
904L - SUPER AUSTENITIC STAINLESS STEEL
7 Layer Tank
1st layer – 316L / 316Ti / 2205 Duplex / 904L Stainless Steel.2nd layer – CCC Power (Climate Control Coating).
3rd layer – Fire Retardant Thermal Insulation.
4th layer – High Density Pu ff.
5th layer – GL Panel.
6th layer – Scrim Wall.
7th layer – 304 Austenitic Stainless Steel.


Guide To Select Steel
Austentic
- Supply and Ground waters
- Chloride Level < 200 Ppm
- Grade Name: 304
- Nearest EN 1.4301/UNS 30400
Surgical
- Supply and Ground waters
- Chloride Level < 500 Ppm
- Grade Name: 316L
- Nearest EN 1.4401/UNS 31603
Surgical
- Supply and Ground waters
- Chloride Level < 800 Ppm
- Grade Name: 316Ti
- Nearest EN 1.4571/UNS 31635
Duplex
- Brackish Waters
- Chloride Level < 1000-3600 Ppm
- Grade Name: 2205
- Nearest EN 1.4462/UNS 32205
Super Austentic
- Brackish & Sea Waters
- Chloride Level: 3600-26000 Ppm
- Grade Name: 904L
- Nearest EN 1.4539/UNS N08904
Know Your Steel
General Characteristics:
304 is most popular and versatile austenitic stainless steel grade with excellent corrosion resistance, formability, deep drawability and weldability.Chemical Composition:
USN/EN | ASTM | % C | % Mn | % S | % P | % Si | % Ni | % Cr | % n | |
---|---|---|---|---|---|---|---|---|---|---|
UNS S30400 | 304 | Min | – | – | – | – | – | 8.0 | 17.5 | – |
EN 1.4301 | Max | 0.07 | 2.00 | 0.030 | 0.045 | 0.075 | 10.5 | 19.5 | 0.10 |
Mechanical Properties:
Grade | Mechanical properties | UTS(MPa) | Ys(MPa) | %EL | HARDNESS(HRB) |
---|---|---|---|---|---|
304 | ASTM A240 | ≥ 515 | ≥ 205 | ≥ 40 | ≤ 92 |
Physical Properties:
Density | Modulus of Elasticity (Gpa) | Thermal Conductivity (W/m OC) | Thermal Expansion coefficient (um/m/°C) | Electrical Resistivity (uQm) |
---|---|---|---|---|
7910 | 195 | 16.3 | 17.3 | 0.72 |
Applications:
Grade 304-Transport, chemical, petrochemical and fertilizers industries, dairy, food processing, pharmaceutical industries, hospital equipment, cryogenic vessels, households as utensils & appliances, heat exchangers, machinery in paper, pulp, textile and beverage industries; architectural applications like panels, curtain walls, roofing etcCorrosion Resistance:
These grades exhibit excellent resistance to wide range of atmosphere and corrosive media like petroleum, food, pharmaceutical, textile etc.Corrosion resistance of core range austenitic
Core range austenitic have good corrosion resistance and are suitable for a wide range of applications.Uniform corrosion
Uniform corrosion is characterized by a uniform attack on the steel surface in contact with a corrosive medium. The corrosion resistance is generally considered good if the corrosion rate is less than 0.1 mm/year (0.004 in/year)Pitting and crevice corrosion
Pitting and crevice corrosion typically occur in acidic or neutral chloride solutions. Core range products have good resistance to these types of corrosion.Atmospheric corrosion
Core range austenitic stainless steels offer good resistance to atmospheric corrosion in applications where superficial surface staining from incipient pitting or crevice corrosion is usually undesirable.General Characteristics:
316L is low carbon version of 316 for excellent intergranular corrosion resistance during welding. 316Ti is Ti stabilised 316 for excellent intergranular corrosion resistance at elevated temperature.Chemical Composition:
USN/EN | ASTM | %C | %Mn | %S | %P | %Si | %Ni | %Cr | %Ti | %Mo | %N | |
---|---|---|---|---|---|---|---|---|---|---|---|---|
UNS S31603 | 316L | Min | – | – | – | – | – | 10.0 | 16.0 | – | 2.00 | – |
EN 1.4404 | Max | 0.030 | 2.00 | 0.030 | 0.045 | 0.75 | 14.0 | 18.0 | 3.00 | 0.10 | ||
UNS 31635 | 316Ti | Min | – | – | – | – | – | 10.0 | 16.0 | 5*(C+N) | 2.00 | – |
EN 1.4571 | Max | 0.08 | 2.00 | 0.030 | 0.045 | 0.075 | 14.0 | 18.0 | 0.70 | 3.00 | 0.10 |
Mechanical Properties:
Grade | Mechanical properties | UTS(MPa) | Ys(MPa) | %EL | HARDNESS(HRB) |
---|---|---|---|---|---|
316L | ASTM A240 | ≥ 170 | ≥ 485 | ≥ 40 | ≤ 95 |
316Ti | ASTM A240 | 205 | 515 | ≥ 40 | ≤ 95 |
Physical Properties:
Grade | Density | Modulus of Elasticity (Gpa) | Thermal Conductivity (W/m OC) | Thermal Expansion coefficient (um/m/°C) | Electrical Resistivity (uQm) |
---|---|---|---|---|---|
316L | 7980 | 193 | 16.3 | 15.9 | 0.72 |
316Ti | 7980 | 193 | 16.3 | 15.9 | 0.72 |
Applications: 316L
Food processing, chemical and petrochemical equipment, brewery equipment, laboratory equipments, heat exchangers, chemical transportation containers.Applications: 316Ti
Its excellent for coastal architectural paneling and mining screens.Corrosion Resistance: 316L
These grade exhibits excellent resistance to wide range of atmosphere and corrosive media like petroleum, food, pharmaceutical, textile etc.Corrosion Resistance: 316Ti
316Ti has much better Corrosion resistence, having titanium the Stainless Steel is harder having super corrosive resistence.Structural Fire Resistance 316Ti
For example, the titanium-stabilized 316Ti has higher strength values at elevated temperatures than other stainless steel products.Uniform corrosion
Uniform corrosion is characterized by a uniform attack on the steel surface in contact with a corrosive medium. The corrosion resistance is generally considered good if the corrosion rate is less than 0.1 mm/year (0.004 in/year)316L / 316Ti have good resistance to uniform corrosion in many organic and inorganic chemicals. The addition of molybdenum enhances the alloy’s corrosion resistance in many acidic environments. Austenitic stainless steels that contain molybdenum are therefore sometimes denoted as ‘acid-proof grades’.
Pitting and crevice corrosion
Pitting and crevice corrosion typically occur in acidic or neutral chloride solutions. This range of products provide excellent resistance to pitting and crevice corrosion. Resistance to these types of corrosion is enhanced by increasing the steel’s chromium, molybdenum and nitrogen content. Nickel reduces the pitting propagation rate and facilitates repassivation after pitting corrosion has started.Atmospheric corrosion
Austenitic stainless steels offer good resistance to atmospheric corrosion in applications where superficial surface staining from incipient pitting or crevice corrosion is usually undesirable.These products can normally be used in moderately aggressive industrial and coastal areas.General Characteristics:
Standard Duplex Stainless steel 2205 (UNS 532205) is the most widely used duplex stainless steel comprising almost 80% of duplex stainless steel market. This alloy provides be er corrosion resistance than 316L and 316Ti in various environments and has an added advantage of higher yield strength thereby helping in material savings.Chemical Composition:
USN/EN | %C | %Mn | %S | %P | %Si | %Ni | %Cr | %Mo | %N | |
---|---|---|---|---|---|---|---|---|---|---|
S32205 | Min | – | – | – | – | – | 4.50 | 22.0 | 3.0 | 0.14 |
Max | 0.030 | 2.00 | 0.020 | 0.030 | 1.00 | 6.50 | 23.0 | 3.5 | 0.20 | |
EN 1.4462 | Min | – | – | – | – | 4.50 | 21.0 | 2.5 | 0.10 | |
Max | 0.030 | 2.00 | 0.035 | 0.045 | 1.00 | 6.50 | 23.0 | 3.5 | 0.22 |
Mechanical Properties:
Mechanical properties | Product Form | Thickness Max | UTS(MPa) | Ys(MPa) | %EL | HARDNESS(HRB) | Impact Toughness |
---|---|---|---|---|---|---|---|
UNS S32205 | – | – | 655 min | 450 min | 25 min | 293 BHN | – |
EN 1.4462 | Cold Rolled | 8 | 700-950 | 500 min | 20 min | 293 BHN | – |
Hot Rolled | 13.5 | 460 min | 25 min | 293 BHN | 100(long) min | ||
Plate | 75 | 640-840 | 460 min | 25 min | 293 BHN |
Applications:
Chemical industry: Sour gas piping, Heat exchanger, tanks and vessels for chloride containing media.Oil and Gas industry: Piping and process equipment, offshore structures Cargo tanks in ships for transport of chemicals.
Flue gas desulphurization systems, Electrostatic precipitators, Pulp and Paper industry: Digester.
Corrosion Resistance:
This alloy provides excellent corrosion resistance and pitting or crevice corrosion even in salty sea water environment.General Characteristics:
904L is an Super Austenitic Stainless Steel with high Nickel (25%) and Molybdenum (4.5%) providing good corrosion resistance to stress corrosion cracking in severe chloride environment. Low carbon content of 904L improves its welding characteristic by good resistance to intergranular corrosion. Annealed 904L provides excellent toughness even at sub-zero temperature. It contains a combination of chromium and molybdenum which provides it an improved level of resistance to pi ing and crevice corrosion by chlorides compared to 316L Stainless Steel. The copper addition provides added resistance to reducing media such as hot phosphoric acid and dilute sulfuric acid.Chemical Composition:
USN/EN | % C | % Mn | % S | % P | % Si | % Ni | % Cr | %Mo | % n | %Cu | |
---|---|---|---|---|---|---|---|---|---|---|---|
UNS N08904 EN 1.4301 | Min | – | – | – | – | – | 23.0 | 19.0 | 4.00 | – | 1.00 |
Max | 0.020 | 2.00 | 0.035 | 0.045 | 1.00 | 28.0 | 23.0 | 5.00 | 0.10 | 2.00 |
Mechanical Properties:
Mechanical properties | UTS(MPa) | Ys(MPa) | %EL | HARDNESS(HRB) |
---|---|---|---|---|
UNS N08904 | 490 min | 220 min | 35 min | 90 HRB max |
Physical Properties:
Density | Modulus of Elasticity (Gpa) | Thermal Conductivity (W/m OC) | Thermal Expansion coefficient (um/m/°C) | Specific Heat(J/Kg OC) | Electrical Resistivity (uQm) |
---|---|---|---|---|---|
7950 | 195 | 11.5 | 15.6 | 450 | 95.2 |
Applications:
– 904L is widely used in chemical industries for components such tanks and other products used in handling sulphuric and phosphoric acid.– Fertilizer production equipments.
– Bleaching equipments in pulp and paper industry.
– Heat exchangers handling sea water.
Corrosion Resistance:
This alloy provides excellent general corrosion resistance and pi ing or crevice corrosion that is usually higher than 316 Stainless Steel. 904L provides very good resistance to sulphuric acid, phosphoric and acetic acid. Resistance to chloride Stainless Steel. 904Lprovidesverygoodresistancetosulphuricacid,phosphoricandaceticacid.Resistancetochloridestresscorrosioncracking depends on the percentage of nickel, with 25% nickel 904L o ers more resistance stress corrosion cracking compared to an 8% nickel alloy like 304 Stainless Steel.Heat Treatment:
904L in annealed state provides excellent impact strength at room temperature and at cryogenic temperatures.Technical Specifications
Capacity(Ltr) | Diameter(mm/inch) | Height with stand(mm/inch) | Inlet Fitting(inch) | Over Flow(inch) | Outlet Fitting(inch) | Drain(inch) |
---|---|---|---|---|---|---|
100 | 630/25 | 680/26 | 1" | 1" | 3/4" | 3/4" |
200 | 700/28 | 980/38 | 1" | 1" | 3/4" | 3/4" |
300 | 700/28 | 1330/52 | 1" | 1" | 3/4" | 3/4" |
400 | 700/28 | 1650/65 | 1" | 1" | 3/4" | 3/4" |
500 | 1070/42 | 1170/46 | 1" | 1" | 1" | 1" |
750 | 1070/42 | 1600/63 | 1" | 1" | 1" | 1" |
1000 | 1070/42 | 1830/72 | 1" | 1" | 1.5" | 1.5" |
1500 | 1420/56 | 1880/74 | 1" | 1" | 1.5" | 1.5" |
2000 | 1530/60 | 2060/81 | 1" | 1" | 2" | 2" |
2500 | 1530/60 | 2200/87 | 1" | 1" | 2" | 2" |
3000 | 1700/67 | 2060/81 | 1" | 1" | 2" | 2" |
4000 | 1700/67 | 2550/100 | 1" | 1" | 2" | 2" |
5000 | 1700/67 | 3120/123 | 1.5" | 1.5" | 2" | 2" |
7500 | 2200/86 | 3070/121 | 1.5" | 1.5" | 2" | 2" |
10000 | 2200/86 | 3910/154 | 2" | 2" | 2" | 2" |